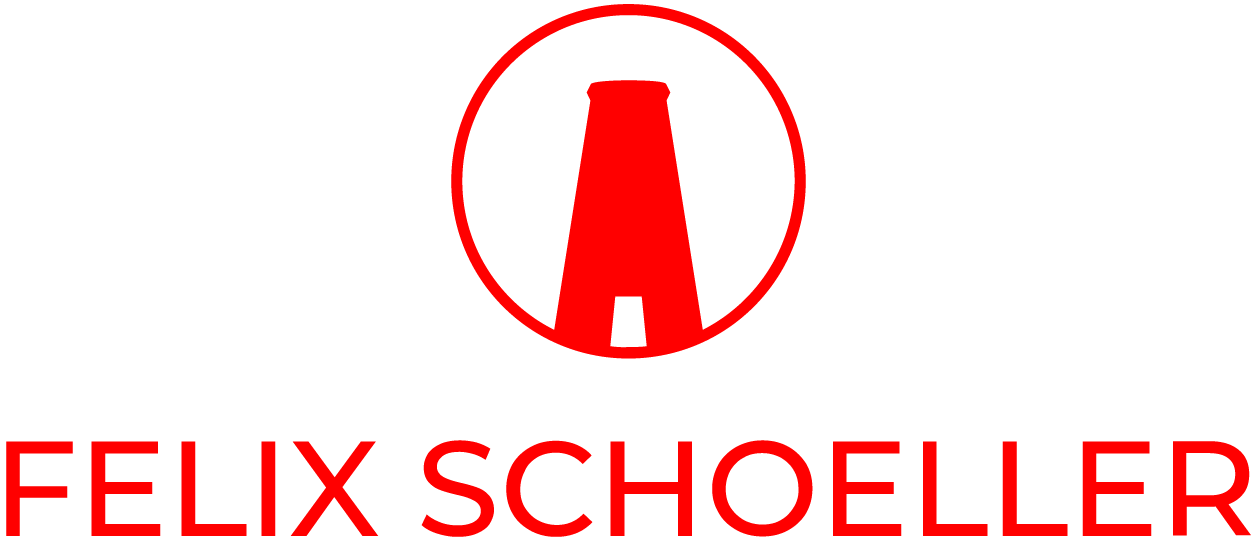
Optimal resource utilization in application development
Paper manufacturer from Osnabrück secures competitiveness through digitization using Simplifier’s low-code technology
1. Initial situation and challenge
Founded in 1895, Felix Schoeller is a family-owned company with global operations. Headquartered in Osnabrück, Germany, the long-established company develops and produces specialty papers and distributes them worldwide. The products are used for photographic applications, digital printing systems, packaging, self-adhesive uses as well as for the industries manufacturing furniture, wood-based materials and wallpaper. For this purpose, the company relies on modern technologies.
However, the company encountered challenges as it sought to optimize its processes and the efficiency of its production lines. There were many manual processes that resulted in time delays and faulty operations. Felix Schoeller’s IT department was looking for a solution to address these shortcomings and increase process efficiency. It was important that the solution was quick and easy to implement.
Felix Schoeller
Although the paper manufacturer was already using low-code platforms, these could not meet the requirements in terms of an optimal interface to SAP. In addition, there was a desire to create applications based on Fiori – but their realization was hindered through the high initial requirements.
Moreover, it was important that the platform had a solid technical basis and a stable framework to ensure high performance and availability. Another crucial factor was excellent support from the provider and a strong community of developers and users, so that support and expertise could be accessed as needed. Overall, flexibility, ease of use, scalability, integration capability, and collaborative partnership were important factors in the selection of the new low-code platform.
2. Solution and results
Felix Schoeller chose Simplifier based on the fact that the platform met all requirements. Connectivity to SAP works flawlessly and the interfaces are documented transparently. Furthermore, the platform enables easy integration with the SAP system and does not require specialized knowledge of different languages, special databases or programming tools.
On top of that, the platform’s flexibility allowed it to be adapted to the company’s specific needs. Through the ability to create individual modules and applications, Felix Schoeller was able to develop customized solutions that are precisely tailored to the company’s exact specifications.
The platform also allowed seamless integration with SAP and other systems and data sources, which facilitated collaboration and data exchange. This was a crucial factor, as Felix Schoeller uses various systems and applications that need to communicate with each other. Beyond the platform itself, however, there were also decisive criteria for Felix Schoeller to choose Simplifier:
“The community, variety of materials and courses, and plethora of templates made our decision to go with Simplifier a lot easier. This gave us a good idea of how the platform works and allowed us to realistically assess the range of possibilities.”
The first application was implemented within a short period of time in close cooperation between Felix Schoeller and Simplifier. This one was particularly important and intended to demonstrate the rapid feasibility of an integrated app in the existing warehouse management system.
“The first application for booking goods received, in which we could directly register incoming stock, was realized in just one day with Simplifier.”
Read more about Felix Schoeller’s Digital Goods Receiving App here.
In just nine days, another application, the Gasometer app, was implemented, resulting in substantial savings when purchasing gas. Based on production planning data from SAP, the app precisely calculates the required amount of gas for the company’s own power plant. This enables Felix Schoeller to precisely control the purchase of resources and determine the actual resource requirements. Against the backdrop of the current energy situation, this is particularly important to ensure conscious use of resources.
By introducing Simplifier, Felix Schoeller was able to streamline its business processes and accelerate them. By mapping the processes digitally, manual work steps and potential sources of error were eliminated, resulting in greater efficiency and faster handling of processes.
Thanks to the implemented applications, the break-even point for the Simplifier platform was reached within one year.
With just one of the applications created with Simplifier, Felix Schoeller is already recording savings of almost €20,000 per month. In the long term, an ROI of 1:4 is expected.
“We reached break-even within one year. And that includes the time of enabling and training. This outcome shows both that the Simplifier technology is state of the art and that the enabling process helped our team to use the platform efficiently very quickly.”
3. Collaboration
The start of the collaboration was accompanied by an enabling service from the Simplifier team. This provided Felix Schoeller’s employees with the necessary knowledge for the successful use of the low-code platform. As a result, two of the planned applications were already implemented together within just two months.
” Thanks to the ideal combination of technology and the competent onboarding by the Simplifier team, which was necessary for us, we had a fantastic start – this enabled us to implement our first projects quickly and efficiently. The support during the initial implementation allowed us to create the first application quickly and smoothly.”
4. Outlook
In total, Felix Schoeller plans to further expand the use of Simplifier. On the one hand, the intention is for as many departments as possible, such as logistics, purchasing or even power plant operations, to benefit from the advantages of the digital applications. Accordingly, the backlog is well filled. The advantages are gradually getting better known throughout the company.
Specifically, in the coming months, the company will implement applications in the areas of freight charges, order picking, sales, and maintenance. The goal is not just to replace Excel tools and expensive end devices, but above all to create applications that minimize the time and effort required to handle the relevant processes and eliminate data transfer errors by integrating them with SAP.
Furthermore, Felix Schoeller also wants to implement the approach of Citizen Development in the long term regarding the use of Simplifier in order to enable the departments to (co-)design their digital solutions.
Want to read the whole Success Story?
Simply enter your email address and receive more information about this customer’s challenges and solutions.
You are currently viewing a placeholder content from HubSpot. To access the actual content, click the button below. Please note that doing so will share data with third-party providers.
More Information